Why Use Rigid-flex PCBs Instead of Flex PCBs in Electronics Projects?
- Share
- Issue Time
- Sep 13,2022
Summary
With the ever-increasing demand for small devices, flexible and rigid-flex PCB circuit boards are widely used in PCB manufacturing and assembly, where they are small, fast, and flexible. Ability to do better at optimal levels without breaking.
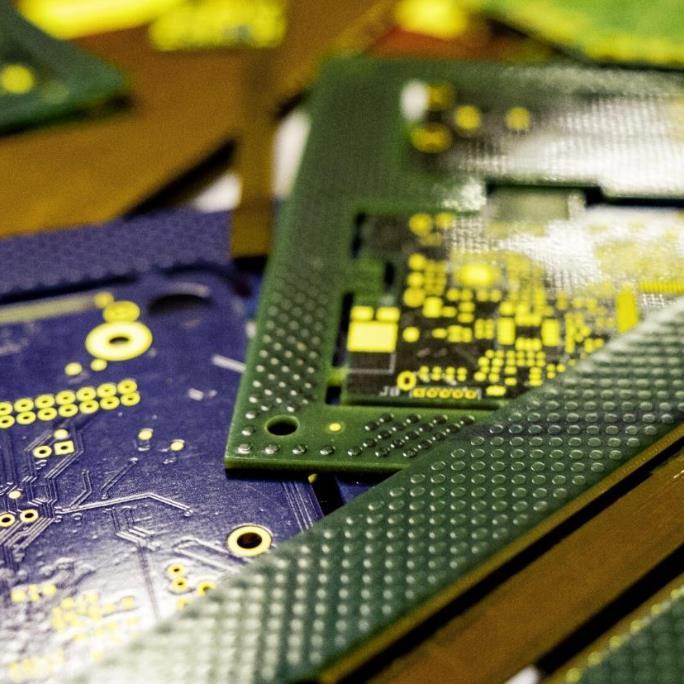
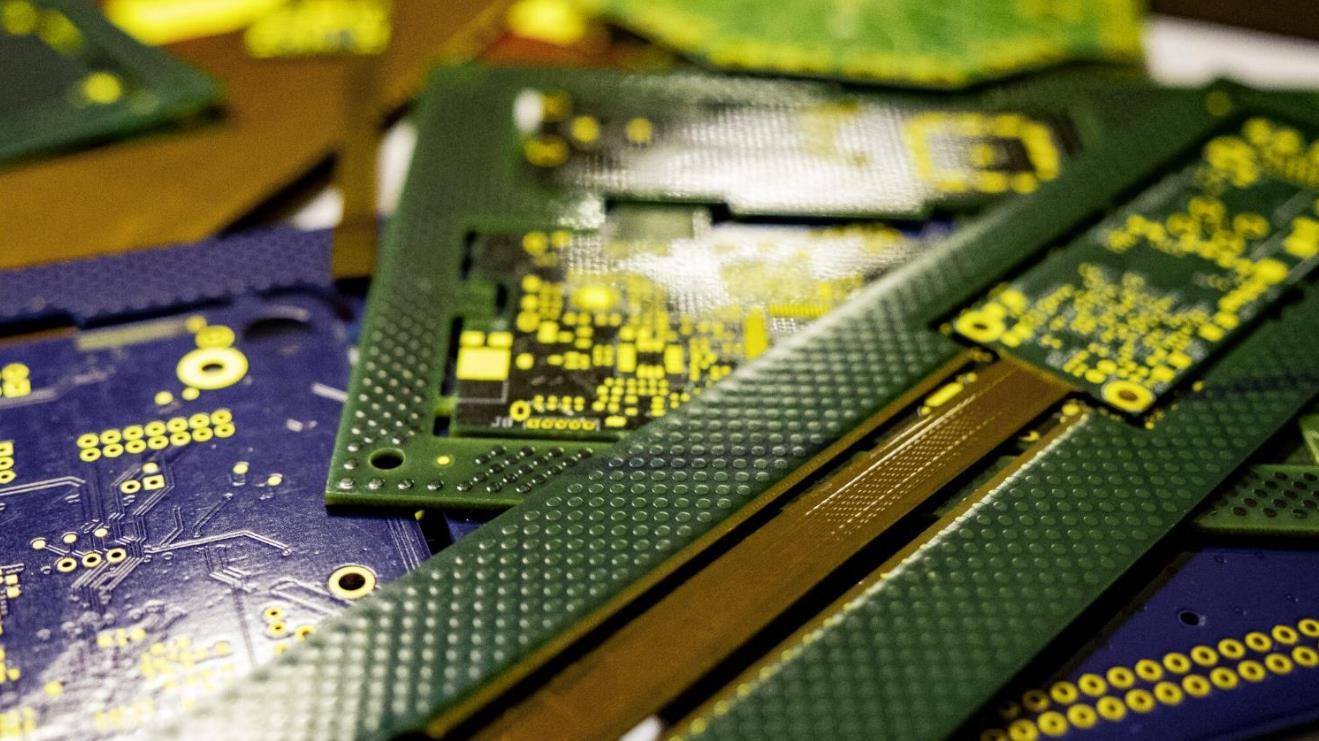
When it comes to PCBs, many people think of rigid PCBs, and rigid PCBs are the most common form of printed circuit manufacturing. However, as the demand for smaller devices continues to increase, PCB manufacturers and engineers are challenged to achieve higher performance in smaller and smaller form factors to meet customer demands. Therefore, there are two main types of circuit boards widely used in PCB manufacturing and assembly, which are small, fast, and flexible, such as flexible PCBs and rigid-flex PCBs.
Needless to say, unlike conventional rigid PCBs, flexible circuit boards are rolled from copper and similar materials with the main goal of providing adequate flexibility and resistance to bending. But rigid-flex PCBs consist of flexible printed circuit boards and rigid PCBs and have multiple layers of flexible and rigid technologies that allow them to do better at optimal levels without the risk of breakage.
What is a flexible PCB?
A flexible printed circuit board, also known as a flexible printed circuit board, is a patterned arrangement of printed circuits and components using flexible materials with or without a flexible cover layer. Flexible electronic components can be manufactured using the same components as rigid printed circuit boards, however, allowing the circuit board to meet the needs of the necessary shape during its application.
The benefits of flexible PCBs
Reduced space and weight: Flexible PCBs can reduce space by more than 50% and weight by 95% while maintaining the functionality and reliability of the circuit board.
Minimize errors: Flexible PCBs reduce wiring errors because mechanical connectors are eliminated and changes in assembly methods are reduced.
Durability: They can handle changing external forces and improve shock and vibration resistance, such as flexibility, weight reduction, and the number of interconnects in a PCB.
Signal integrity: Flexible PCBs can work well in a wide range of environments, so the signals function well regardless of external conditions, which improves the signal reliability of the PCB.
Heat dissipation: The thinner the flexible PCB material, the larger the surface area to volume ratio, and the better the heat dissipation effect.
Low cost: Flexible PCBs are cost-effective because fewer assembly steps are involved when creating a flexible PCB.
High density: Thin layers and smaller components mean that flexible PCBs can allow for higher circuit densities.
What is a rigid-flex board?
Rigid-flex PCB is a circuit board composed of flexible PCB and rigid PCB, and rigid-flex PCB has multi-layer flexible and rigid technology, so it can do better at an optimal level without the risk of breaking. Rigid-flex PCBs can be fully customized to meet the application needs of the various vias, materials, and track widths used.
As you know, the rigid-flex board is not in a fragile state, on the contrary, the rigid-flex board is in a stable state of the curve. A rigid-flex PCB is shaped like a spring and returns to its original state if you stretch or compress it.
The advantages of rigid-flex PCB
Reliable interconnection;
Reduce logistics and assembly costs;
One rigid part for mounting components and one flexible part for movement;
Very reliable and space-saving thanks to the connection without connectors;
Easy assembly due to flexibility and lack of connector connections;
With integrated interconnection, there will be no mis-installation, which can prevent mis-installation during maintenance;
There are many options for impedance control rails; impedance control of rigid and flexible sections is possible.
Rigid-flex PCB applications
Rigid-flex PCBs have a variety of applications in a variety of accessories and devices that are used on a daily basis. One of the most obvious uses is in smartphone applications. Currently, it requires a very thin but powerful smartphone, which is only possible with rigid-flex technology.
Another well-known application of rigid-flex PCBs is in various computer electronics. Hard drives are one of many components that utilize rigid-flex technology. It can catch up with the ever-increasing write speeds of today's computers. Using a rigid-flex PCB for hard drives is great because it allows the hard drive to cool down.
In consumer products, rigid-flex PCBs not only maximize space and weight but also greatly improve reliability, eliminating the need for many solder joints and fragile wiring that is prone to connection problems. However, rigid-flex PCBs can be used in almost all advanced electrical applications, including test equipment, tools, and automotive.
Why choose a rigid-flex board?
Rigid-flex PCBs are a way to eliminate electronic designs, connectors, flex cables, and discrete wiring. Compared to other circuit boards, it has excellent electrical performance because the circuit is an integral part of the overall structure. All electrical and mechanical connections are contained inside the rigid-flex PCB, so it can provide electronic designers with greatly improved service reliability and electrical performance.
The reason why rigid-flex PCB is superior to rigid PCB and flexible PCB is that it has the advantages of reliability, weight reduction, strength, and space-saving, while rigid-flex PCB is more expensive. In addition, rigid-flex PCBs provide the best benefits of rigid-flex PCBs in one solution.
The application of rigid-flex PCB:
High-density applications. Sometimes it is difficult to accept all the cables and connectors required for an electronic PCB design in a small enclosure. Needless to say, rigid-flex PCBs can be folded into tiny profiles, thus saving even more space in these cases.
High-reliability applications. Connectors with flex cables can fail if the components are exposed to excessive or repeated shock or high vibration. Rigid-flex PCBs offer high reliability even under shock applications and extreme vibrations.
Five or more rigid PCBs. If your application will ultimately involve five or more rigid boards interconnected using flex cables, an integrated rigid-flex solution is often the best and most cost-effective option.
The above briefly describes the application of the benefits of rigid-flex PCB boards. If you want to customize PCB boards, please contact us.
Singo is a professional custom PCB board manufacturer. The products involve home appliances, digital products, industrial control, medical equipment, etc. After years of hard work, we have established long-term cooperative relationships with some internationally renowned companies. Some of our products are often required to operate in harsh environments where quality and reliability are paramount. With years of experience, we have won a good reputation from customers in the field of electronic production with reasonable prices, abundant resources, and punctual delivery.