Improve PCB Quality with Uniform Copper Distribution
- Share
- Issue Time
- Nov 2,2022
Summary
All printed circuit boards use copper for the core and traces in all layers. Inconsistent distribution of copper in the layer stack can cause many problems such as bending, twisting, and warping.
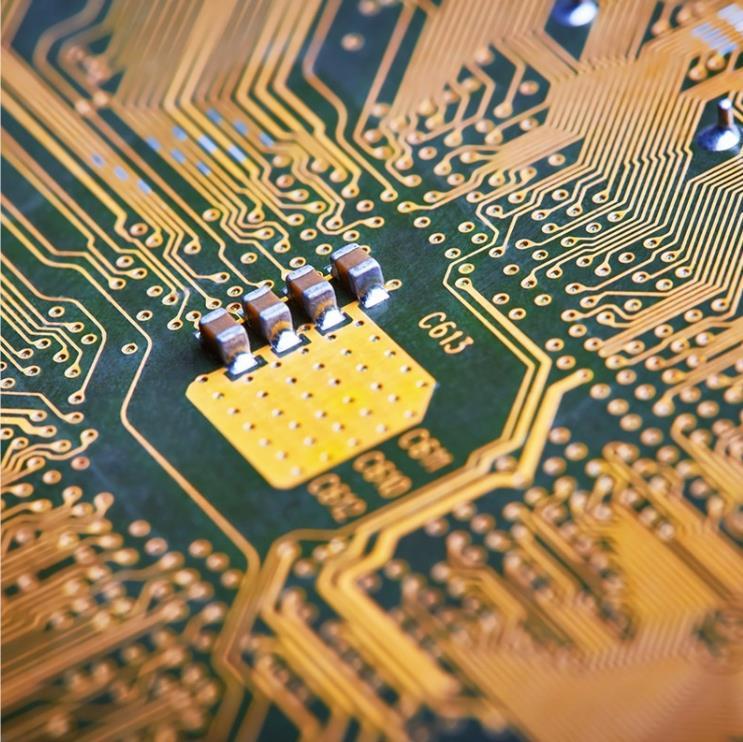
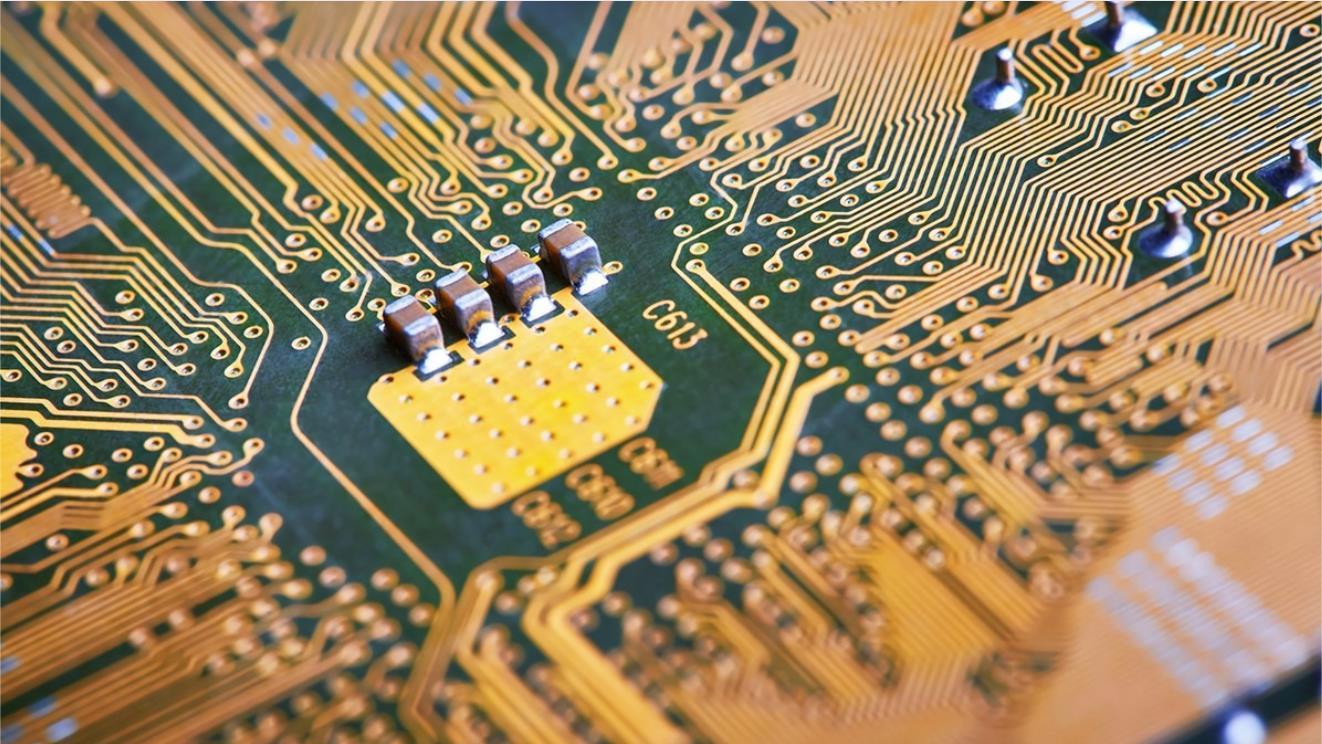
All printed circuit boards use copper for the core and traces in all layers. Even the outermost layer contains copper as the main component. According to Rush PCB USA, the inconsistent distribution of copper in a layer stack can cause many problems such as bending, twisting, and warping.
Bow
Due to inconsistent copper coverage, the PCB may acquire spherical or cylindrical curvature. A PCB with a bow will experience pressure or tension on its surface depending on the direction of the bend. Depending on the degree of bending, the board may experience uneven current circulation, increasing EMI/EMC effects and reducing reliability.
Twist
Ideally, all corners of the PCB are on the same plane. Inconsistencies in copper distribution can distort the PCB, causing two diagonal corners to lift up and the other two to move down. The twisting of a PCB board creates stress in all its layers.
Warping
Inconsistencies in copper distribution can lead to various types of warpage or bending and twisting in the PCB. This is also known as the potato chip effect. Warpage can not only cause uneven current distribution across the board, but it can also cause cracks in the traces and leads where components are mounted, resulting in current interruptions and serious interruptions in board functionality.
Causes of PCB warpage
During manufacturing and assembly, circuit boards go through several stages of heating and cooling. These can occur during pressing, etching, electroplating, application of solder mask, and soldering of components. In each of these processes, the copper and substrate material in each layer expand and contract at different rates.
The substrate material is mostly uniform across the layers of the PCB, while the copper distribution may not be equally uniform. As the two materials expand and contract at different rates, the PCB can deform. Repeated deformation can cause permanent deformation of the circuit board.
Uniform copper distribution prevents PCB warpage
Although manufacturers manufacture PCBs according to international standards such as IPC 600A (Rev.G), several factors can cause PCBs to warp, bend and twist. To some extent, the type of surface finish, substrate material, etc. all contribute, but the main contribution is the inconsistent copper distribution.
Following some ground rules during the layout stage can help reduce or even prevent PCB warpage later on. Designers must ensure that conductor traces are evenly distributed across the layer to avoid copper nests.
Designers must follow the same considerations on the axis of symmetry between two or more layers. For example, if a layer requires a large amount of copper fill, the symmetrical opposing layer must also have a similar copper fill to balance the former. It is necessary to fill the open area with copper in both layers to create a balance.
In addition to similar copper filings in the symmetric layers, the flatness and thickness of the copper in these layers are also important. Therefore, uniform distribution is important not only on the surface but also on the volume of the copper. This is because the uneven distribution of copper in each layer of the multilayer PCB, uneven distribution, or uneven thickness of copper above and below the horizontal center of the board may cause an imbalance in its mechanical stability.
Uneven copper distribution affects vias
Uniform copper distribution results in greater mechanical stability and reduces the likelihood of board distortion during fabrication and assembly. In addition, the even distribution of copper also aids the plating process as it results in a uniform thickness of the plating, not only on the surface of the copper tracks but also on the barrels where the through holes are plated.
Uneven copper distribution affects dielectric thickness
The uniform distribution of copper allows for more accurate control of the dielectric thickness between copper layers. Manufacturers use prepreg as glue to hold the layers together. This is a flexible fiberglass-based material impregnated with semi-cured epoxy resin.
When manufacturers stack these layers, they put prepreg sheets between them. When the layers are pressed and heated, the prepreg liquefies and flows to fill the gaps between the copper features, ensuring that air is not trapped inside the board. Any trapped air will heat up during assembly and begin to deflate. This can cause the board to delaminate or eject components from the board.
The uniform distribution of copper ensures that the amount of prepreg used is controlled, resulting in a consistent dielectric thickness.
Ensuring uniform copper distribution in the PCB
Designers can use the free tool PCB Visualizer available online to verify that the copper distribution in their PCBs will result in a uniform plated surface. The tool uses copper distribution and density to calculate the plating index of the outer layer. If the plating index is low, it indicates a large variation in copper thickness.
This tool divides the PCB surface into cells. It calculates the copper density of each cell and compares it to the average copper density of the entire board. Based on this information, it assigns a color to each cell. Cells marked in blue are at risk of under-plating, while cells marked in red indicate that they are at risk of over-plating.
A plating index of 1 indicates that the plating process will provide uniform plating. Values less than 1 indicate uneven copper plating, with red and green areas as highlights. A plating index below 0.4 indicates a manufacturing issue that affects board reliability and quality, while increasing scrap rates.
The manufacturing process of a PCB inevitably leads to variations in the copper thickness on the board. This is because the electroplating process does not result in a uniform build-up of the copper metal lattice. Additionally, almost every manufacturing step is followed by a cleaning process that removes a small amount of copper. Additionally, manufacturers start with a base copper thickness with about a 10% tolerance.
Added copper thief
Manufacturers often add copper-stealing features to PCBs. They do this because the DFM process may indicate uneven copper distribution on the board. Their main purpose is to adjust the copper distribution in a layer to make it more uniform. This allows for more predictable etching and plating. Since the etching and electroplating processes require immersion of the copper-clad layer in a chemical bath, regions with different copper densities will have different rates when electroplating and etching.
For example, a small copper feature on a circuit board with very little copper adjacent to it will be prone to over-etching and over-plating, resulting in unpredictable dimensions of the feature.
Typically, for additional plating, manufacturers use an electrolytic plating process that must pass an electric current through the copper cladding. Here, copper features in sparsely populated areas, including pads, traces, and plated through holes, tend to be overplayed compared to copper features in denser areas where current distribution is more uniform.
In conclusion
The basic idea of uniform copper distribution across PCB layers is to improve quality and reliability by reducing the likelihood of board warpage during the manufacturing and assembly stages. The uniform distribution of copper also allows for more uniform etching and plating.
The above briefly introduces how to improve PCB quality through uniform copper distribution. If you want to customize or buy PCB boards, please contact us.
Singo is a professional custom PCB board manufacturer. Products involve home appliances, digital products, industrial control, medical equipment, etc. After years of hard work, we have established long-term cooperative relationships with some internationally renowned companies. Some of our products are often required to operate in harsh environments where quality and reliability are paramount. With years of experience, we have won a good reputation from customers in the field of electronic production with reasonable prices, abundant resources and punctual delivery.