The Importance of PCB Burn-in Testing
- Share
- Issue Time
- Nov 16,2022
Summary
Without inspection and testing, the board will not meet its design requirements. This article discusses one of the most commonly used PCB inspection methods: burn-in testing.
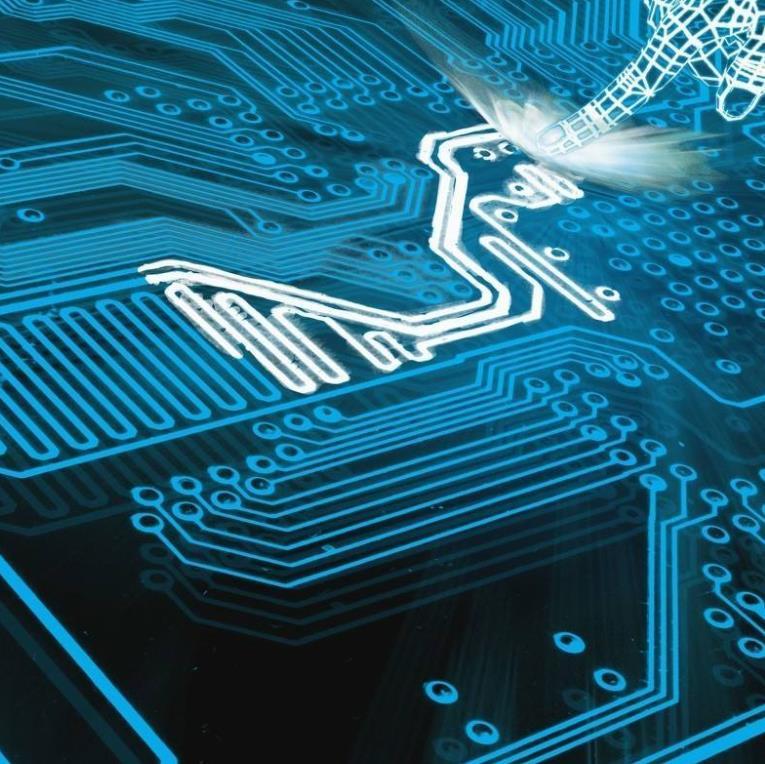
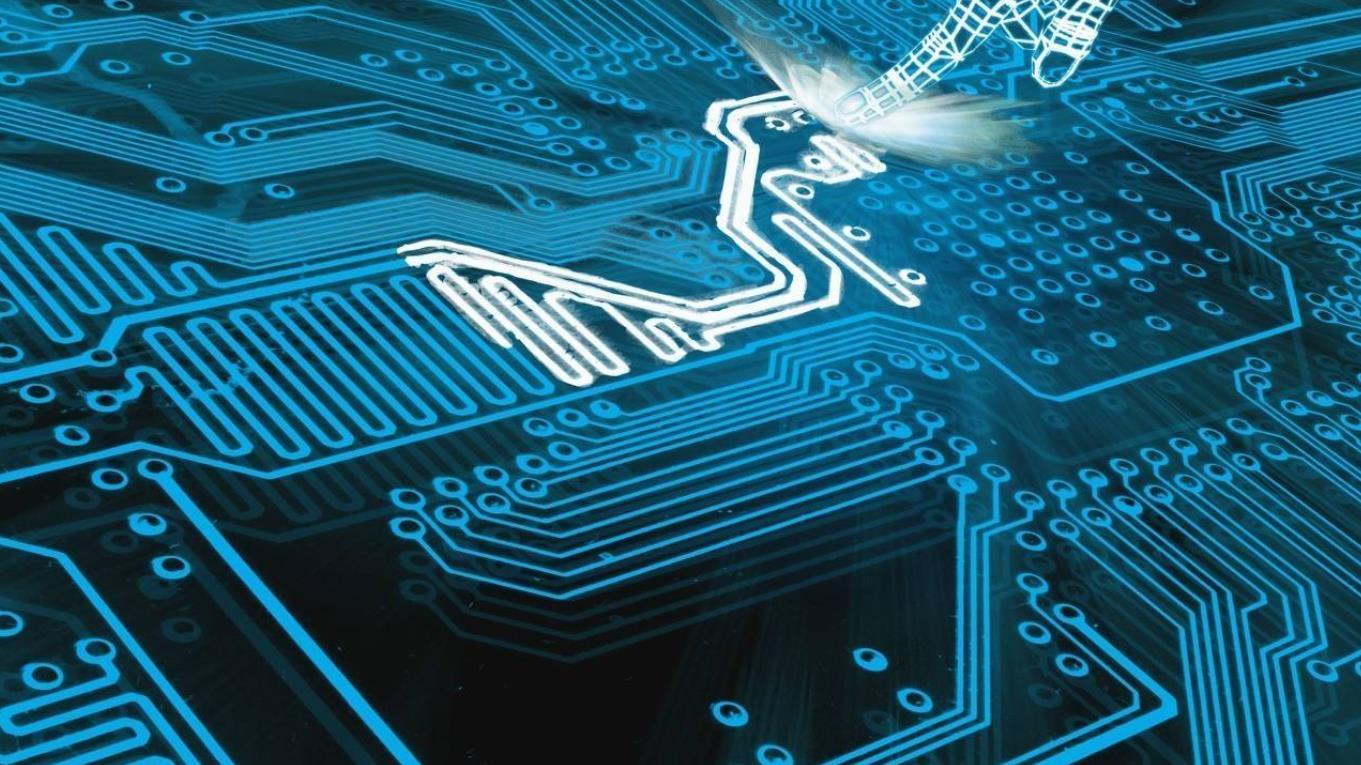
Most PCB designs produced today have mechanical tolerances of 10% or less. SMT boards for cell phones and other wireless devices are a good example, where lead pitch and trace width are limited to 0.4mm and 0.25mm, respectively. Due to the high precision requirements of the design, the need to inspect and test the PCB cannot be underestimated.
Without inspection and testing, the board will not meet its design requirements. This is true of all industries that use PCBs, especially aerospace, defense, military, and other industries that require high precision. Several types of test/inspection techniques have evolved in the PCB manufacturing sector with the increasing emphasis on testing and inspection with the demand for higher quality components. This article discusses one of the most commonly used PCB inspection methods: burn-in testing.
What is Burn-in Test?
Burn-in testing (also known as stress testing) is one of the most critical processes in PCB assembly. This is an important procedure that gives manufacturers the opportunity to ensure their products are free of defects before they leave the factory. Burn-in tests are usually carried out for several days. During the test cycle, the product operates over a range of high and low temperatures and voltages. The standard does not specify hours but should be sufficient to detect abnormal behavior or defects.
PCB burn-in testing is performed by using a dedicated burn-in chamber that operates at high temperatures. Before testing, the manufacturer develops a test plan that includes specifications for the number of samples, run time, temperature, and other variables used in the process.
Reasons for Burn-in Testing
The three main goals of PCB burn-in testing are to detect latent failures, determine the time to failure, and measure MTBF (Mean Time Between Failure). The following points confirm why you should not ignore this test method.
Testing plays an important role in product reliability. The sooner a problem is caught, the less expensive it is to fix it. Aging can also help you determine the useful life of your components. Boards with higher failure rates tend to fail faster during burn-in. Therefore, you can predict the actual life of the board with the help of burn-in testing.
These tests are designed to stress components to detect weak points and failure modes.
Thanks to this testing method, manufacturers can reduce returns and warranty issues while also stabilizing production. This saves the entire development team time, money, and effort.
If you don't take the time to do burn-in testing, you risk creating a defective product and also losing your reputation in the market.
This test is also carried out during the manufacturing process to verify that the process is performed correctly. It allows the manufacturer to arrange additional inventory if the board fails the test. Burn-in also helps reduce costs associated with post-production failures.
Additionally, burn-in testing helps ensure that the PCB meets the customer's performance specifications. For example, if a manufacturer needs to know if their PCB can withstand high temperatures and high humidity levels, doing this kind of testing would be the best way to test it.
As the complexity of electronic systems continues to increase, failure rates have been on the rise. PCB burn-in testing is a technique that helps reduce failure rates by exposing electronic products to harsh environments. Overall, the role of a well-inspected printed circuit board (PCB) is clear.
It provides a stable foundation for electronic components and forms the backbone of all electrical and electronic products, whether mobile phones or computers, airplanes, cars, and more. So it goes without saying that PCB manufacturers who are keenly checking their boards at every step of production play an important role in making these devices with the expected level of quality. Therefore, when you are looking for a PCB manufacturer partner for your next project, please consider working with a company like Singo, and if you want custom PCB boards, please contact us.
Singo is a professional custom PCB board manufacturer whose products involve home appliances, digital products, industrial controls, medical equipment, etc. After years of hard work, we have established long-term cooperative relationships with some internationally renowned companies. Some of our products are often required to operate in harsh environments where quality and reliability are paramount. With years of experience, we have won a good reputation from customers in the field of electronic production with reasonable prices, abundant resources, and on-time delivery.