Everything You Wanted to Know About PCB Materials
- Share
- Issue Time
- Feb 14,2023
Summary
With the rapid development of electronic design, the correct selection of the material for the PCB board will affect the quality of the signal passing through the board. Read on to learn more.
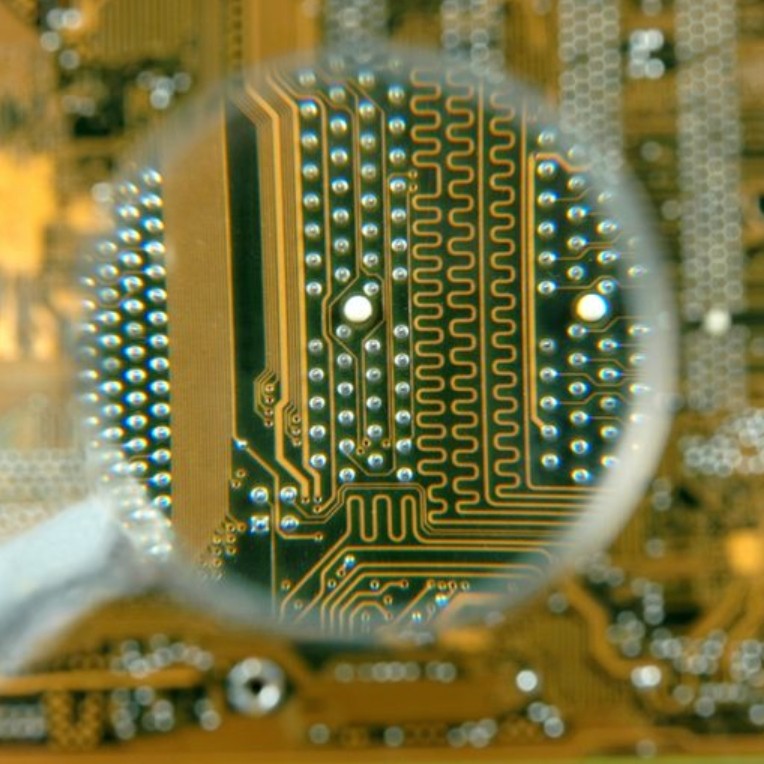
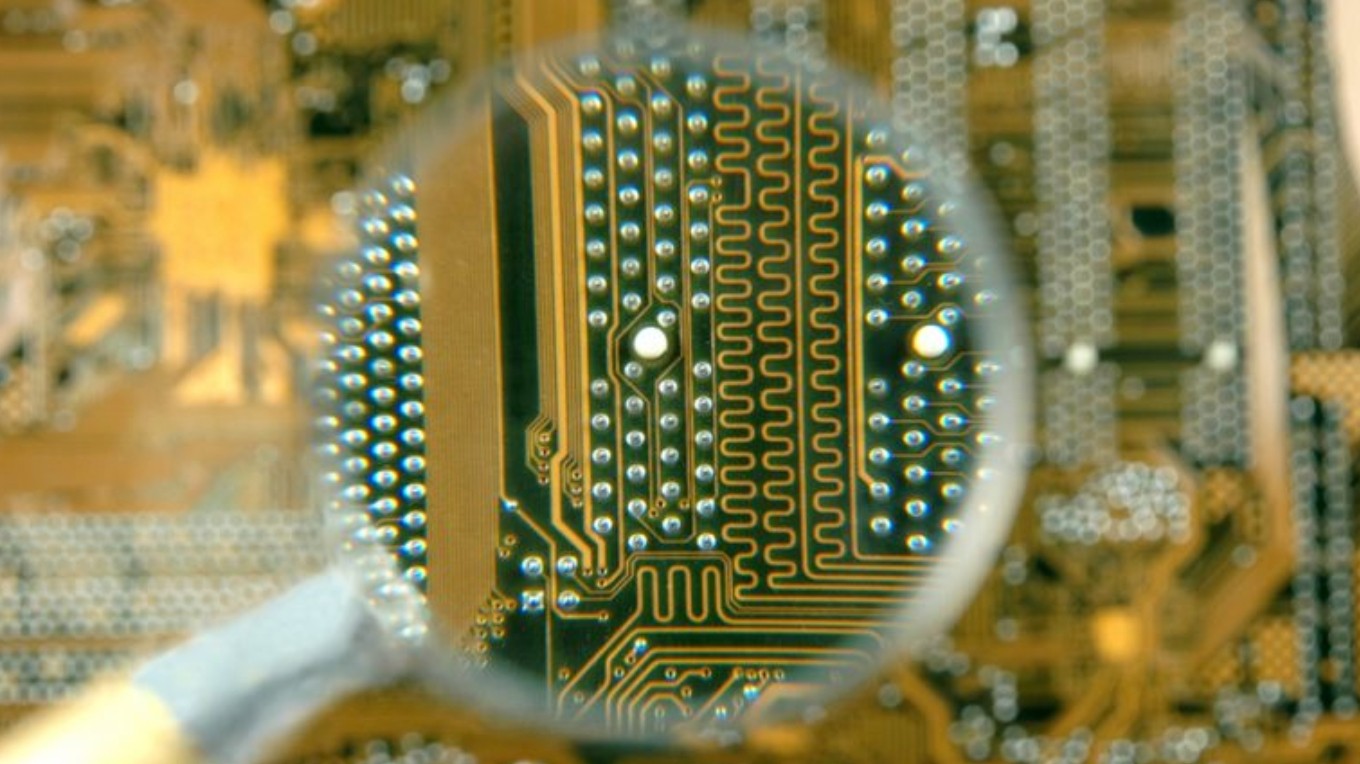
Singo always starts designing PCBs by choosing the right material. The goal is always to use the correct material to manufacture a PCB while meeting electrical and thermal requirements. As most electronic designs move to high speeds, the proper choice of materials can affect the quality of the signal passing through the board. Therefore, the choice of circuit board material determines the performance and quality of the final product.
The Composition Material of PCB
To make a circuit board, a fabricator needs three things:
Prepreg
This is a glass cloth-reinforced board impregnated with resin. Typically, this is a B-stage material that is not fully cured. Adhesive material allows bonding to other laminates or foils. Prepreg manufacturers offer a variety of epoxy resin combinations and glass braids.
Copper Foil
The copper foil on the outermost layer of the PCB forms the conductive medium through which electrical signals and current flow between components. Manufacturers create electrical connections on the board by etching copper foil to create copper traces on the PCB.
CCL
The core made by the circuit board manufacturer makes up the prepreg, which is laminated and cured with copper foil on both sides. Manufacturers offer a variety of cores with different thicknesses, glass weave types, and epoxy properties. PCB designers define the combination requirements that best suit their application.
To manufacture copper-clad laminates, manufacturers use suitable interwoven fiberglass glass cloth and impregnate it in epoxy resin. They semi-cure this impregnated cloth and bond multiple layers to achieve the desired thickness, adding copper foil on the outside. This forms a copper-clad laminate.
Important Properties of PCB Materials
When selecting materials for board construction, designers must consider four fundamental properties of PCB materials.
Chemical Properties
The chemical properties of PCB materials are important because they determine the quality and reliability of the product. The two most important chemical properties are:
Hygroscopicity - This is the ability of a material to resist absorbing water from its surroundings. Moisture absorption can cause the PCB to gain weight and lose some electrical properties.
Conductive Anodic Wire Resistance – This is the ability of the PCB material to resist electromechanical migration to form a wire. These filaments are conductive and may cause a short circuit on the PCB. Designers must use CAF-resistant materials.
Mechanical Behavior
The mechanical properties of a PCB material determine its ability to withstand external loads and stresses while maintaining its properties. Three important mechanical properties are:
Modulus of Elasticity - A measure of a material's stiffness that defines the amount of force required to deform the material.
Flexural Strength - A measure of a material's ability to withstand mechanical stress without breaking.
Tensile Strength - A measure of the maximum stress a material can withstand without breaking when pulled apart from its sides.
Thermal Performance
The thermal properties of a PCB material determine its ability to withstand extreme temperatures while maintaining its properties. The four important thermal properties are:
Thermal Conductivity - A measure of a material's ability to conduct heat. The thermal conductivity of dielectric materials is quite low compared to that of copper foil. Therefore, copper foil can remove more heat than the dielectric material of PCB.
Coefficient of Thermal Expansion – The rate at which a PCB material expands or contracts when heated or cooled. PCB materials can expand or contract in three dimensions. Typically, materials have a very low ability to expand or contract in the X and Y directions. This is because the woven glass limits expansion in the X and Y directions. However, the ability of the material to expand or contract in the Z direction is an important parameter.
Substrates typically have a higher CTE in the Z direction than copper, which can cause interconnect problems as the material heats up or cools down. Therefore, a low CTE along the Z direction is a desirable property for PCB materials.
Decomposition Temperature - This is the temperature at which the PCB material begins to lose its mass or begins to chemically decompose irreversibly. Since most PCB materials are assembled at temperatures between 200 and 260℃, where the solder melts, the decomposition temperature of the PCB material must be above this range.
Glass Transition Temperature - This is the temperature range at which a PCB substrate begins to change from a rigid, glassy state to a rubbery, deformable, softer state. This change is reversible as the board material cools.
Electrical Properties
The electrical properties of a PCB material determine its ability to maintain signal integrity around the frequency of operation. Two parameters are important here:
Dielectric Constant – The relative permittivity of a material. For most materials, the dielectric constant varies with frequency, decreasing as frequency increases. To maintain proper signal integrity at high-frequency operation, suitable materials must have a low dielectric constant that does not vary with frequency over a wide range.
Dissipation Factor – As frequency increases, power is lost in the dielectric material. This results in signal attenuation. PCB materials suitable for high-frequency operation must have a low and flat frequency dissipation factor.
Signal Loss Mechanisms in PCB Materials
At high-frequency operation, PCB material properties can affect signal integrity. Engineers overcome this problem by selecting the correct type of substrate and copper foil. Signal loss in PCBs is mainly due to losses in the dielectric and copper foil. Therefore, these two materials play a major role in causing PCB signal loss.
Dielectric Loss
The dielectric material constitutes the polarized molecules. A time-varying signal passing through the copper traces generates an electric field that causes the molecules to vibrate. Due to these vibrations, the dielectric heats up, causing the dielectric loss portion of the signal loss. As molecular vibrations increase with frequency, they cause higher losses in the dielectric. Materials with a low dissipation factor exhibit lower loss levels with increasing frequency.
Copper Loss
Eddy currents formed within copper traces carrying time-varying signals cause skin effects, forcing most of the current to flow to the outer surfaces of the traces. This effectively reduces the area through which current flows, causing the signal to face higher resistance. Skin effect increases with frequency. If the surface finish of the copper traces is nickel, most of the signal may flow through the nickel layer, increasing signal loss.
Designers can reduce the skin effects by using wider traces, which increase the cross-sectional area of the trace. But increasing the width of the traces is not always possible.
Since most of the outer surface of the traces carries the signal, the roughness of the surface also affects the resistance and thus their loss. Therefore, a smooth copper surface reduces signal loss.
Designers must select copper foil based on the following characteristics:
Thickness - Typically, copper thickness varies from 0.3 mils (0.25 oz) to 7 mils (5 oz).
Purity - Electronic grade copper is approximately 99.7% pure.
Copper Dielectric Interface Profile -- Low profile provides lower copper loss for high-frequency signals.
Basic PCB Material Types
There are four basic PCB material types based on dissipation factor and speed of operation:
Normal Loss and Normal Speed
These are the most common types of PCB materials. Isola FR370HR and FR-4 series materials fall into this category. Due to the high dielectric loss, these materials also do not exhibit a flat permittivity vs. frequency dependence. Therefore, these materials are only suitable for digital or analog applications up to a few gigahertz.
Medium Loss and Medium Velocity
Medium-speed materials have a slightly improved frequency dielectric constant and half the dielectric loss of normal-speed materials, making them suitable for applications approaching 10 GHz.
Low Loss High Speed
These materials have a very low dielectric loss and a flatter dielectric constant over frequency, making them suitable for applications operating between 10–30 GHz. Low-loss and high-speed materials also generate lower levels of unwanted electrical noise than other materials.
Very Low Loss and Very High Speed
These materials are suitable for RF/microwave frequency applications. They exhibit the smallest dielectric loss and the flattest dielectric constant over frequency. They are suitable for operating frequencies of 20 GHz and above.
Types of Copper Foil
Calendered Copper Foil
This type of copper foil is mostly used by manufacturers to make flex PCBs, as they are processed by rolling between heavy rollers and are therefore very thin. The smooth surface and horizontal grain structure produced by rolling make rolled copper ideal for low loss and high speed PCBs.
Electrolytic Copper Foil
This type of electrodeposited copper foil has a rough surface and vertical grain structure and is suitable for rigid PCB applications operating at normal losses at normal speeds.
Thin Copper Foil
Organic additives or levelers added to electrodeposited copper foil plating baths help reduce roughness.
Best Practices for PCB Material Selection
Choose materials with low hygroscopicity
Select CAF-resistant material
Choose a tightly woven substrate
Always match the CTE
Do not use FR4 for high-frequency and high-speed designs
Follow IPC standards:
IPC-4101C – IPC Standard Specification for PCB Substrates for Rigid Multilayer Boards.
IPC-4103 – IPC standard specification for PCB substrates for high frequency/high-speed applications.
IPC/JPCA-4104 — IPC standard specification for PCB substrates for HDI and micro via boards.
IPC-4204 — IPC Standard Specification for Flexible and Metal-Clad Substrates.
In Conclusion
Reputable PCB manufacturers such as Singo have been using specialty high-frequency/high-speed circuit materials for decades for various reasons. These materials have several unique properties compared to more traditional PCB materials. By understanding these properties, OEMs and PCB manufacturers can not only improve circuit performance but also greatly benefit from it. If you want to order PCB boards, please contact us.
Singo is a professional custom PCB board manufacturer. The company is mainly engaged in PCB assembly and OEM/ODM electronic manufacturing services. Products include household appliances, digital products, industrial controls, medical equipment, etc. After years of hard work, we have established long-term cooperative relationships with some internationally renowned companies. Some of our products are frequently required to operate in harsh environments where quality and reliability are critical. With many years of experience, we have won a good reputation from customers in the field of electronic production with reasonable prices, abundant resources, and on-time delivery.