Is PCB Inspection Required?
- Share
- Issue Time
- Mar 30,2023
Summary
A robust inspection process before concluding the assembly process of a printed board assembly can uncover hidden defects—saving assemblers valuable time while preventing costly repairs later.
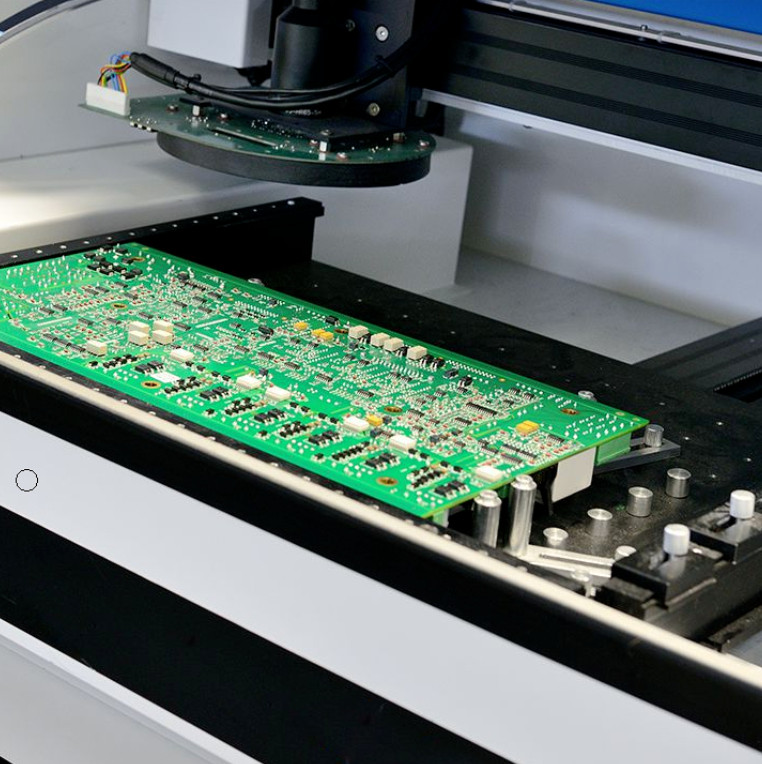
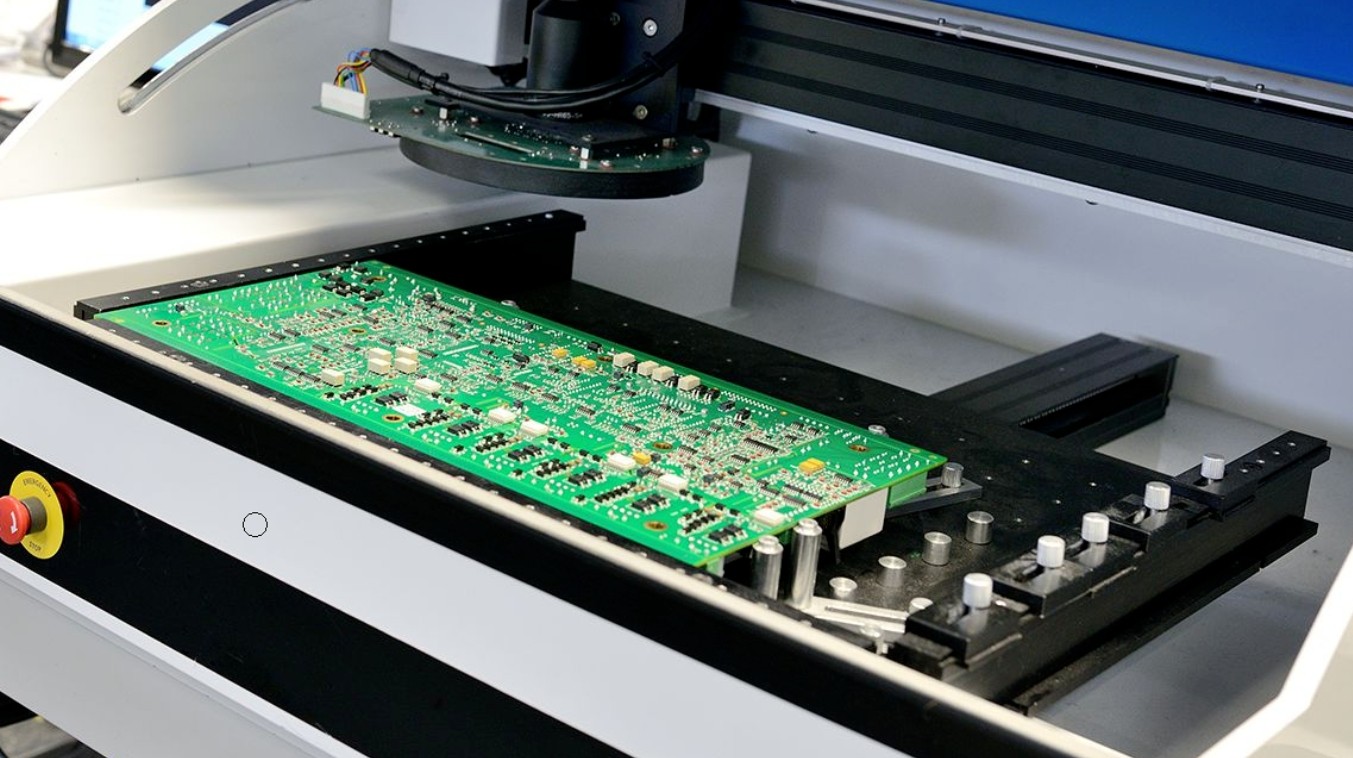
Singo recommends a robust inspection process before concluding the assembly process of printed board assemblies. That's because the inspection process uncovers hidden defects—saving assemblers valuable time while preventing costly repairs later.
Types of PCB Inspection Processes
Depending on the requirements and customer needs, there are many types of inspection processes an assembler can perform on a PCB assembly. Some of them are:
Manual PCB Inspection: This involves manually inspecting components and inspecting them for defects.
Automated Optical Inspection (AOI): Using an optical system to capture images of components and compare them on a computer to identify defects.
Automated X-ray Inspection (AXI): Optical systems may not be suitable for complex and dense assemblies. Optical systems that use visible light cannot see hidden solder joints under BGA chips. To see these hidden joints, x-rays are necessary.
X-ray Inspection: Without the use of X-rays, complex circuit boards with multiple layers cannot be inspected. Inspection with X-rays helps to find defects in buried vias and defects in inner layers.
Defects Discovered During Inspection
Some common defects that are easily found by PCB inspection methods are:
Footprint Error: Complex boards may have multiple types of ICs with different footprints. Designers download the necessary footprints from a CAD library when designing a board. If the library does not have the correct footprint, the chances of downloading the wrong footprint pattern increase. Manual inspection or AOI methods can easily find such defects because they usually appear on the top or bottom surface.
Defective Blind/Buried Vias: Complex boards using multiple layers use blind and buried vias to interconnect layers. Visual inspection or the AOI process cannot determine the integrity of these vias because they are hidden in inner layers. Using AXI or X-ray inspection methods can help penetrate the substrate to assess the health of hidden vias.
Soldering Defects Under BGA: BGA ICs have solder balls on the bottom that need to be properly soldered to the pads to function. Soldering defects under the IC cannot be detected by manual inspection or AOI because the plastic body of the BGA IC hides the soldering underneath. These defects can only be assessed by AXI or X-ray inspection methods.
Solder Voids: Solder quality is very important for the reliability of PCB assembly. The presence of moisture can cause voids to form in the solder joints. If the void is on the surface of the solder joint, it can be detected by manual inspection or AOI. However, AXI and X-ray inspection is necessary to detect voids under solder joints.
Pinhole Defects: Pinholes in plated through-hole (PTH) barrels often form during the plating process and can cause PTH breakdown, creating electrical discontinuities. The only possible way to detect these defects is to use X-rays.
Missing Components: An incorrectly programmed pick-and-place machine or incorrectly set up SMD reel may prevent the machine from installing certain components. Missing components are easily found by visual inspection of the board and AOI.
Advantages of PCB Inspection
It is clear that PCB inspection is an important process stage that offers several advantages and ensures strict control over assembly quality. An inspection stage in place in the assembly chain can actually help improve the throughput of PCB production. For example, if a particular defect happens to recur, an operator can change process parameters to prevent it from happening again.
The PCB inspection stage may seem like an impediment to the smooth flow of the production line. It may also appear to add cost. However, comparing the time and cost involved in the PCB inspection phase with the time and cost involved in correcting product failures at a later stage will convincingly demonstrate the importance of PCB inspection.
Inspecting the PCB after each process step helps ensure that the correct process parameters are set for consistent quality throughout the production line. Without proper inspection protocols in place, defective boards may reach the OEM and enter the market as defective products. This can lead to costly recalls, resulting in huge damage to the OEM's and assembler's reputation. If the product is a medical device or an automotive part, the damage may be more serious.
Depending on the defect type, mounting PCB inspection and functional testing phases not only ensure adequate board performance but also help maintain acceptable cycle times. Employing the best inspection technology for your assembly project's needs can greatly help ensure the integrity of your PCB.
The above introduces the importance of PCB inspection. If you want to order PCB boards, please contact us.
Singo as a professional custom PCB manufacturer, our products involve home appliances, digital products, industrial control and medical equipment. After years of hard work, we have established long-term cooperative relationships with some well-known international companies. With many years of experience, we have won a good reputation from customers in the field of electronic production with reasonable prices, abundant resources, and punctual delivery. Singo is fully equipped to handle all types of PCB fabrication and assembly. With our state-of-the-art machinery and talented team of experts, we can meet any quality and testing industry standards.