The PCB Assembly Process and What You Should Know
- Share
- Issue Time
- Apr 6,2023
Summary
The PCB assembly process is critical to first-time success. In this article, we'll cover some of the most important PCB assembly process steps and what you should know.
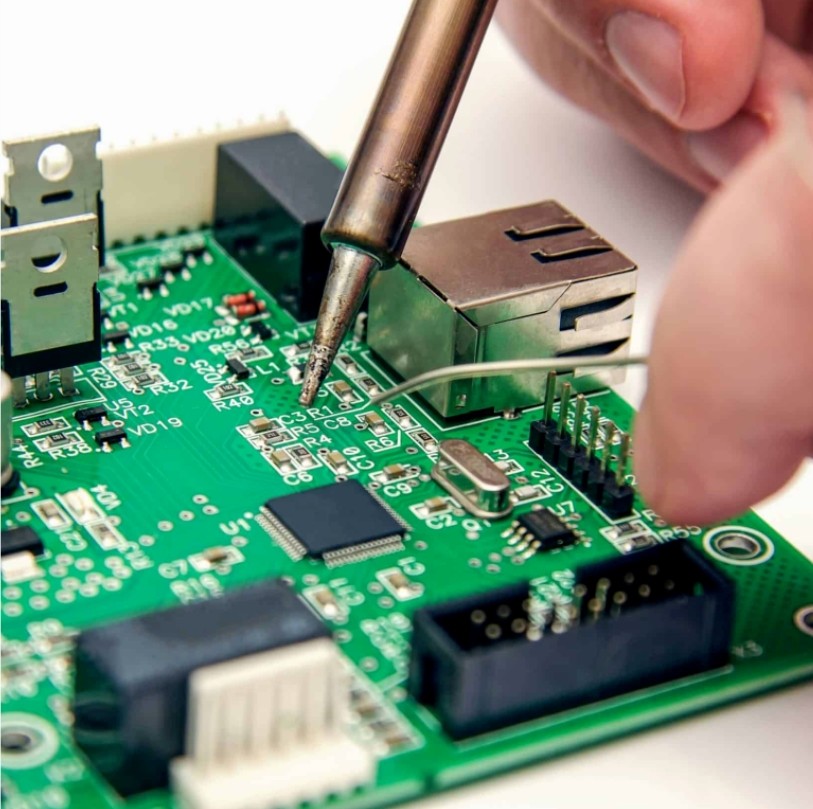
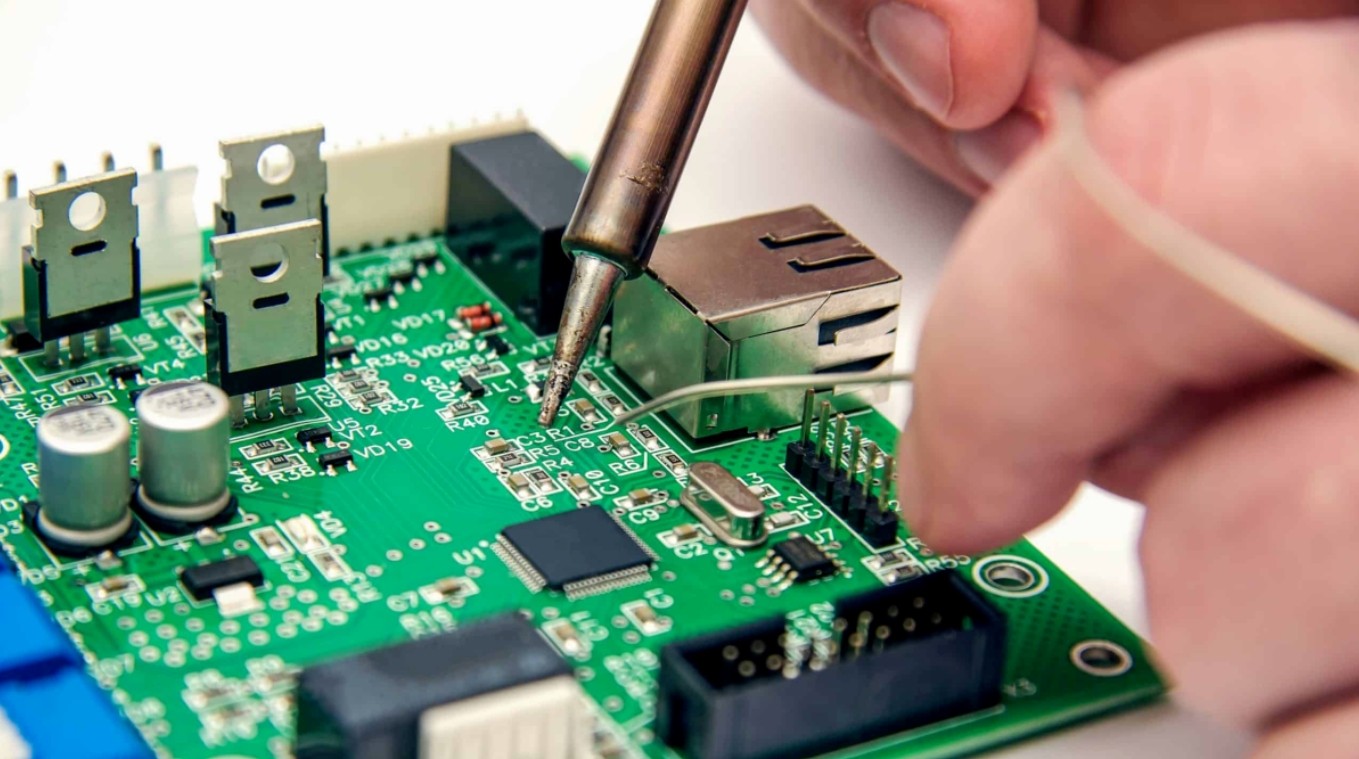
In every electronic device in use today, there is a printed circuit board that makes it run. A PCB is the heart of an electronic device, whether we're talking about a smart speaker in your home, your new smart thermostat, or the digital speedometer in your car. Of course, creating functional electronics requires more than just putting together a bunch of components and resistors.
The PCB assembly process is critical to first-time success. A single misstep here can lead to malfunctions, loss of functionality, and even the threat of an accident. In this article, we'll cover some of the most important PCB assembly process steps and what you should know.
This Is Not Circuit Board Manufacturing
First, understand that the PCB assembly process occurs during a specific period of electronic device development. It's not about manufacturing - it happens first. For example, we will first fabricate the board itself, including all required layers, creating traces, and all other important steps, and then proceed to PCB assembly.
Simply put, PCB assembly is the process of putting everything in one place and creating functionality from multiple components. It takes a freshly fabricated board, adds components and resistors, and then makes sure it works the way it's supposed to.
Learn about PCB Assembly Technology
Assembling a printed circuit board requires more than raw components and a well-designed board. It also requires the right technique. In this case, there are multiple options to choose from, each of which leads to something different. For example, there is Surface Mount Technology (SMT) and the use of manual soldering and placement machines.
While some PCB assembly processes require only one technique, others require a combination of two or more. For example, many circuit boards require a combination of through-hole technology (THT) and surface mount technology. Knowing when, where and how to integrate these technologies is an important consideration when choosing a company to handle your project or production.
It is also important to understand that the PCB assembly steps involved in various technologies are also different. Below, we outline some of the basic steps involved, and how they differ between techniques.
PCB Assembly Process: An Overview
Solder Paste: If you are using a traditional PCB assembly process, the first step is to apply solder paste. Note that this is not the case with THT, but SMT does require paste application and/or printing.
Component Placement: In the traditional PCB assembly process, the next step is to place the components on the board. This can be done manually or with the help of machinery (pick and place systems). In THT assembly, components are placed by hand, which requires incredible precision. During the SMT process, robotic systems place components on circuit boards. Note that automatic placement is much faster than manual placement and is just as accurate.
Reflow Soldering: In the traditional PCB assembly process, the next step is reflow soldering, where the solder is first melted and then re-solidified. The board and all its components run through an oven to heat the solder, which liquefies it and ensures the connection is made before the board is moved into a cooler, where the solder cools.
Note that the THT process does not require solder reflow. Instead, the second step here is to inspect the board and correct component placement. This is due to the manual placement process - visual inspection in conjunction with designing the shipping frame helps ensure placement accuracy.
In the SMT process, reflow soldering also occurs at this time. The board passes through a furnace, melting the solder paste, allowing it to flow as necessary, and then the board passes through a series of coolers that gradually reduce the temperature, solidify the solder on the board and bond the components in place.
Inspection: The next step in the traditional PCB assembly process is a visual inspection of the board, soldering, and components. Note that this step has been performed in both THT and SMT processes.
Through-Hole Part Insertion: Traditional processes require through-hole insertion to be done manually after the reflow and inspection process. Soldering is also often done by hand, but it can also be done using wave soldering.
At this time, wave soldering also occurs during the THT process. The entire board moves over the liquid solder and then through a cooler to solidify the solder.
Note that there are no relevant steps in the SMT process (it's actually done and ends in just three steps, but a visual inspection should still be done to ensure accuracy and reduce the chance of error).
Final Inspection and Cleaning: The final step in the traditional PCB assembly process is to perform a final inspection of the board, solder joints and components, and clean to ensure that debris or excess solder is removed.
Right for Your PCB Assembly Process
While the SMT assembly process is faster and often more accurate than a traditional PCB assembly process or THT process, it is not always the best choice. For example, if you only need to assemble a prototype board, the THT method may be a better choice. Every situation is different, and no one solution will fit all needs all the time.
At Singo, we understand that needs, budgets, and goals vary. We pride ourselves on providing solutions for every customer need. As a professional custom PCB board manufacturer. Our company has specialized in electronic PCB assembly. Since 2006, it has been mainly engaged in PCB assembly and OEM/ODM electronic manufacturing services. The products involve home appliances, digital products, industrial control, medical equipment, etc. After years of hard work, we have established long-term cooperative relationships with some internationally renowned companies.